Anodize
MIL-8625F
TYPE II & TYPE III SULFURIC ACID ANODIZE
Anodizing is an electrochemical process that converts the metal surface into a decorative, durable, corrosion-resistant, anodic oxide finish.
The anodic oxide structure originates from the aluminum substrate and is constructed entirely of aluminum oxide. This aluminum oxide is not applied to the surface like paint or plating, but is fully integrated with the underlying base material, so it cannot chip or peel. It has a highly ordered, porous structure that allows for secondary processes such as coloring and sealing.
Anodizing is accomplished by immersing the aluminum into an acid electrolyte bath and passing an electric current through the medium. A cathode is mounted to the inside of the anodizing tank; the aluminum acts as an anode, so that oxygen ions are released from the electrolyte to combine with the aluminum atoms at the surface of the part being anodized. The anodizing process is essentially a matter of highly controlled oxidation.
We offer Type II Anodize in both clear and black dye finishes up to 12 feet in length. Type II Anodize typically reaches a thickness of .0002”-.0008” dependent upon desired finish.
We also offer Type III Anodize on aluminum alloy material up to 12 feet in length. Natural & black dye finishes are available for components that require a more durable & wear resistant coating than can be obtained with the Type II process. Hard Anodize typically reaches a minimum of .001" thickness.
For more information about anodizing or to request a quote please visit the contact page.
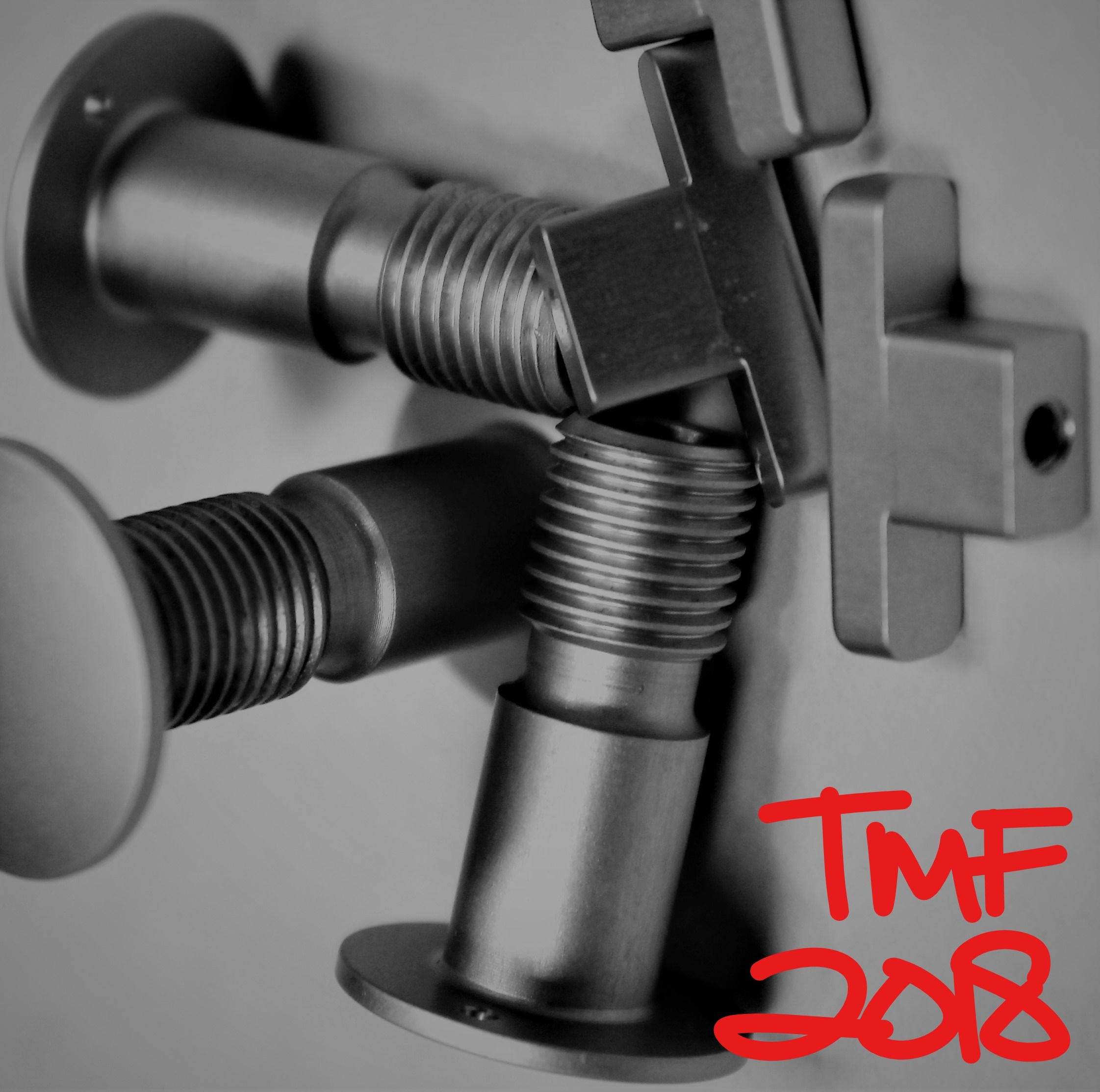
